Background: Joe Claborn has worked with McMurray Hatchery for many years and currently raises started chicks and started pullets for McMurray. Joe is also involved with a project that Bud Wood, president of McMurray Hatchery, initiated to start backup flocks for many of McMurray’s rare breeds during the current Avian Flu outbreak.
This is part 2 of a three-part interview (see part 1 of the interview). We plan to publish part 3 of the interview in the next few weeks.
Q: In addition to caring for the chicks that Bud brought down from Iowa, I know that you also raise and supply started chicks for Murray McMurray Hatchery. Can you tell me more about that?
We raise both started chicks (available for purchase at 4 to 9 weeks of age) and several breeds of started pullets (available for purchase at approximately 15-22 weeks of age) for Murray McMurray Hatchery.
We start by getting an order of chicks from McMurray Hatchery once a month. We normally get somewhere between a thousand and fourteen hundred chicks at a time.
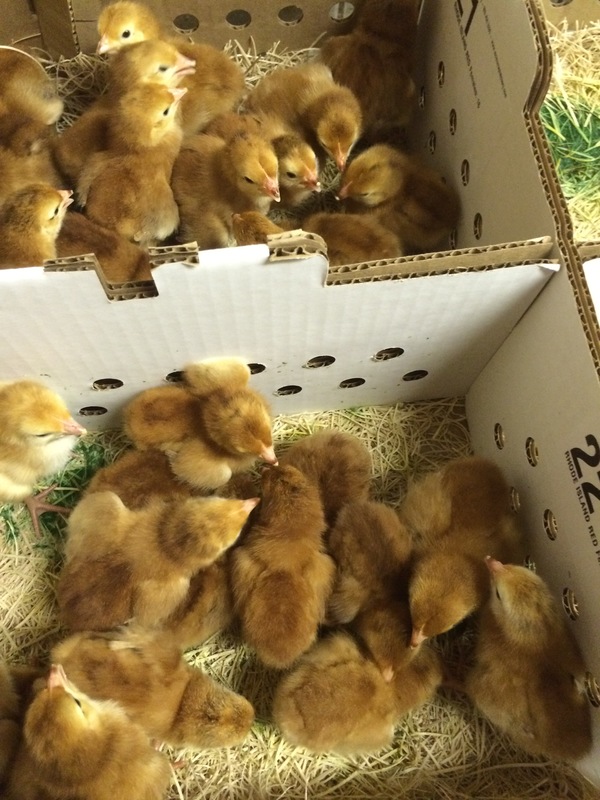
New day old baby chicks received from Murray McMurray Hatchery
When we get the chicks, of course, we do the same things that an owner at home would do. We water each chick and feed them. We always give them some boiled eggs to start with because that’s a very good feed, and it’s what they’re used to. An egg is the last thing the chicks ate before they were shipped, so we start them off with another egg to eat. When the weather is cool, we use warm water in their waterers so the chicks won’t lose body temperature when they first drink. We also use a nutrient supplement in their water to help them get off to a good start.
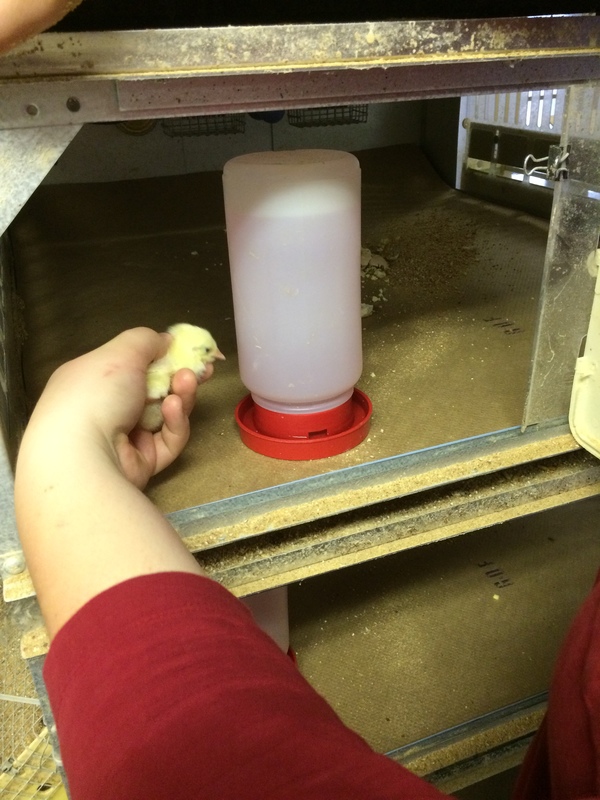
Before turning chicks loose in the brooders, we dip their beaks one by one to teach them where to find water
After we set them up in our brooders, we watch them and take care of them. In four weeks we begin to ship them to customers. We ship them at four weeks, five weeks, six weeks and seven weeks of age. Normally we’ve sold out (or nearly so) by seven weeks, so we’ll do our brown egg layer special on the last week to sell any chicks that remain. Then on the eighth week we’ll have another batch of 1,000 to 1,400 chicks come in and we’ll start all over.
Of the chicks that we brood, we raise three breeds to adulthood: the Red Star, the Black Star and the Pearl White Leghorn. We buy extra of those to make sure we will have enough, since we also sell these same varieties at four, five, six and seven weeks of age. When they get old enough to take out of the brooders, we move them out into our field. There we keep them in ten foot by twenty foot hoop houses. We move these portable coops each week so that the chickens will get fresh grass and soil. We feed and water them and care for them just like somebody would at home — we just have a few more to take care of.
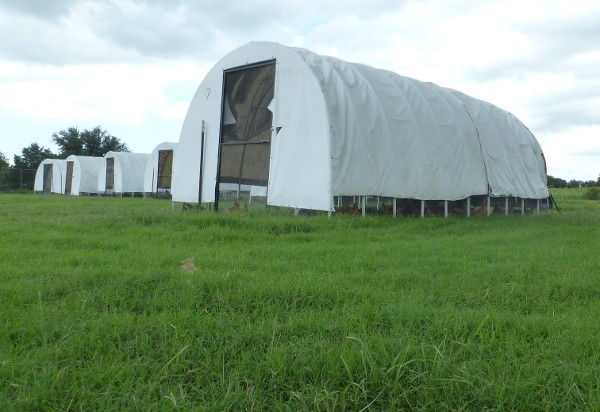
Hoop coops for raising started pullets
Q: How many different breeds do you raise?
Different times during the year, we carry about twenty-seven different breeds.
We don’t carry all of the breeds all the time, but there are a handful of breeds that have the most demand for, so we carry those nearly all of the time. We nearly always have Ameraucanas, Barred Rocks, Pearl White Leghorns, Black Australorps, Cuckoo Marans, Rhode Island Reds, Red Stars, Black Stars, Buff Orpingtons and Silver-Laced Wyandottes. Most of the time we also have Golden-Laced Wyandottes, and we usually have several varieties of Polish.
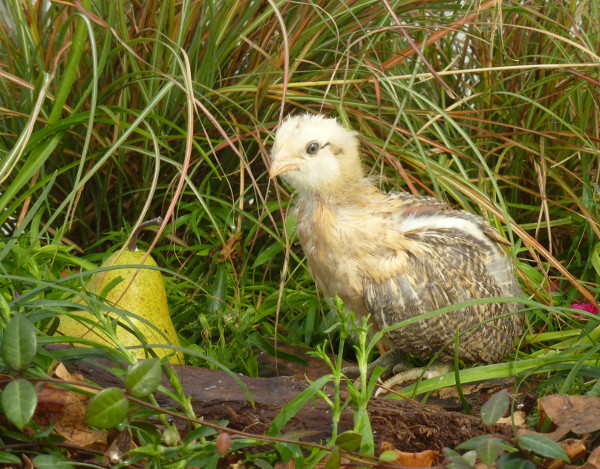
Four week old Ameraucana
Q: How long have you been raising chickens for McMurray?
We’ve been doing it about three years now. And we’ve been raising birds for nearly twenty years, but not nearly as many birds as we’re raising and shipping now.
When we first started, we’d consider ten orders to be a huge week. It was challenging for us. The shipping boxes we were using at the time were one difficulty, so it was a big improvement when we worked with McMurray to design a shipping box that would be better for the birds and easier to work with. The box we came up with has more ventilation for better air flow. It has dividers so the birds can’t peck each other. And it has more room.
It’s also very easy to work with. We can pre-attach the lid halfway onto the box so that as soon as we put the bird in we can close the lid, and unless the bird is very vigorous and really wants to get out, there’s enough friction to keep it from opening. Then after we’ve put the bird in the box, one staple and the box is sealed. Since then, we’ve also developed a smaller box for shipping the four-week-olds.
Nowadays on a big shipping day we ship 100 to 140 orders. It’s nothing like what a large hatchery would ship, but for a small family operation, I feel like we’re doing pretty good.
Q: Can you tell me a little more about your shipping process?
Well, today we shipped out forty-nine orders, which was almost 300 birds. In our cycle of raising chicks, this was our second shipping week, so these birds were five weeks old. We also shipped about 120 started pullets (of the three breeds I mentioned previously). We ship on Tuesdays, and we start preparing the shipping boxes the Friday before to save time on the day of shipping.
Monday night, a group of us — my nephew’s working here now, as are my sons, daughter and daughter-in-law — will look at each order and figure out, based on how many birds are in the order and their ages, how many boxes we’ll need. We put bedding in the boxes and attach the invoice and a bar code that later tells us which order each box is for. By the end of the evening, we have a mountain of boxes that are all ready to go.
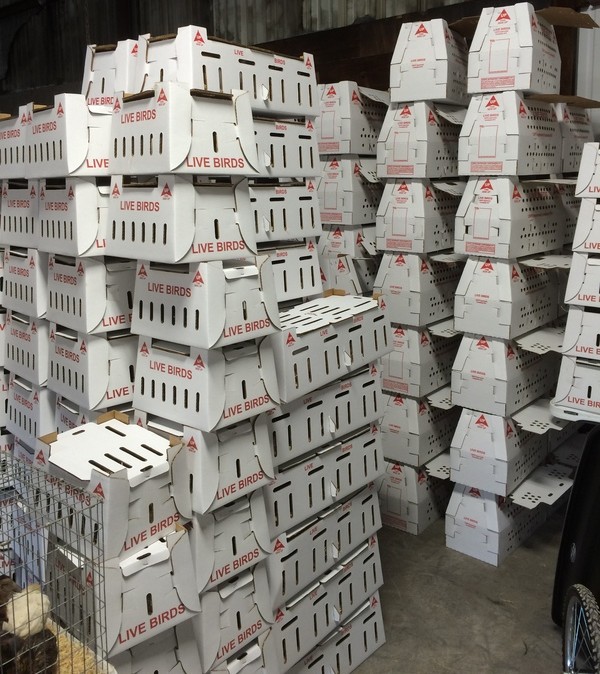
Boxes that have been prepared prior to shipping
The day we ship, we’ll get an early start. Today, I went out to my office at 5AM to begin downloading the shipping information from McMurray into our shipping software. Around 6AM, one of my sons starts cutting cucumbers and cantaloupe to put into the shipping boxes to give the birds the hydration that they’ll need.
Next, I start selecting the birds that we’re going to ship and transferring them from the brooders into small cages that we’ve made, so we can easily transport them to our shipping room.
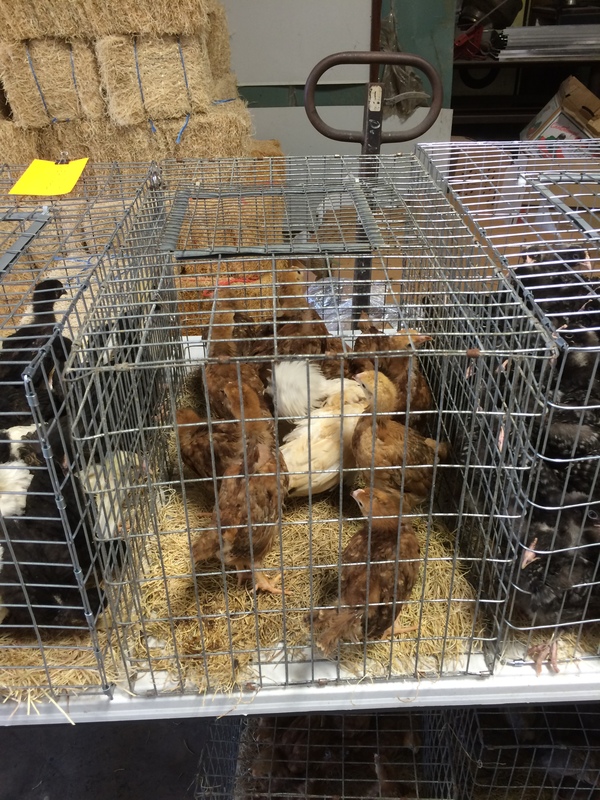
Started chicks that will be soon be loaded into shipping boxes
Once we’ve gathered all of the young birds, we go out into the field and select the started pullets. By this time, it’s about 7AM, and the temperature’s about 80 degrees (F), so once we get the pullets back to the shipping room, we turn on a fan to keep them cool.
We work together to fill each order. We put strapping on the boxes to secure them. We weigh the boxes and print and attach shipping labels. My daughter-in-law inspects each order to make sure it meets our quality standards.
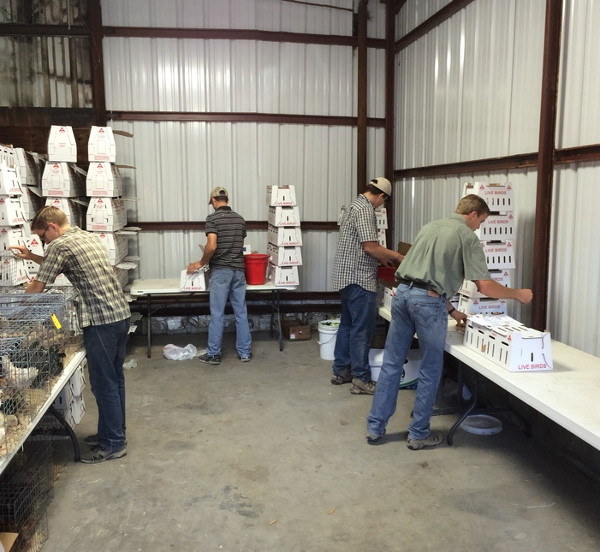
Filling the orders
Once we’ve packaged all the orders, we load our van and drive the birds two hours north to the postal service distribution center in Coppell, just past the Dallas-Fort-Worth airport.
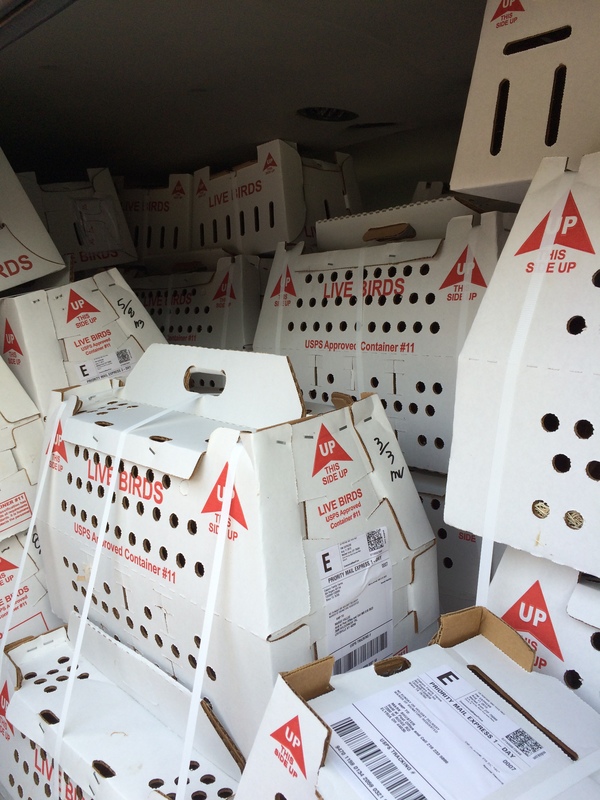
We load the boxes of chicks in our air-conditioned van and drive them to the postal center by the airport.
We drop them off inside the distribution center there because if we just took them to the local postal center, they’d sit on a hot loading dock waiting to be loaded onto the truck, get transported in a truck without air-conditioning and then sit on another hot loading dock in Coppell. By transporting them ourselves in our air-conditioned van, I figure that we save the birds from five hours of unnecessary heat stress.
My birds arrived this morning and all seem happy and healthy after their 48 hours of travel from TX to NC. After ordering my birds (I’m a first time chicken keeper) about two months ago I wondered how they ship. This interview series has been especially interesting to me and made me feel a bit better about ordering them from 1/2 across the country instead of taking my chances with the local Tractor Supply. Thanks!
Good to learn some more about the Chicken industry. I hope the effects of the Avian Flu have been curtailed for this year. Your work helps us maintain our flocks, Thank-You.
Really enjoying this series of interviews! Very interesting to see what happens behind the scenes!
I found your interview very interesting. My last pair of Buff Orpingtons came from your operation in Texas and I was expecting them to come from Iowa. I now know why. All were healthy. Our birds are pets that also provide us with eggs. Your efforts are why people like me purchase from Murry McMurray. Thank you!